In Melbourne, installing a swimming pool is often complicated by one key factor: clay-rich soil. Known for its instability and high reactivity, clay can expand and contract dramatically with moisture changes, causing ground movement that affects pool structures over time.
For homeowners considering a fibreglass pool, a common concern arises: can a fibreglass shell withstand these soil dynamics, or will it crack, bulge, or lift?
This page provides a technical yet accessible breakdown, focused on the specific geological and construction conditions found across Melbourne suburbs. It draws from local builder expertise, case studies, and soil data to help you understand what’s really at stake.
The goal: give you the clarity to make an informed decision—and to anticipate the structural reinforcements and installation techniques required for long-term pool stability.
Why Melbourne’s Soils Require Special Attention
Understanding reactive clay and soil classes across Melbourne suburbs
Melbourne’s geological makeup is far from uniform. Many suburbs sit on what’s classified as highly reactive clay soils—soils that shrink and swell significantly depending on moisture levels. According to the Victorian Building Authority, soil across Victoria is grouped into six classes, ranging from stable (Class A) to highly reactive (Class E). Most of metropolitan Melbourne falls into Class M, H, or E, meaning moderate to extreme movement potential.
This is particularly relevant for pool projects, as soil class dictates how much a foundation will need to adapt and resist shifting forces. Fibreglass pools, being lighter and monolithic in structure, are especially sensitive to uneven soil movement.
Suburbs with higher soil reactivity: Glen Iris, Bentleigh, Malvern East
Several Melbourne suburbs are notorious for having highly reactive clay, posing a real challenge for pool installations. Glen Iris, Bentleigh, and Malvern East frequently appear on engineering reports as areas with Class H to Class E soil ratings, meaning they are subject to significant seasonal ground movement.
These zones experience regular cycles of expansion during wet seasons and contraction during dry spells. Without proper planning, this can lead to structural stress on a fibreglass pool shell, manifesting in bulging, cracking, or misalignment over time.
Builders working in these neighbourhoods often recommend enhanced slab reinforcement and advanced drainage systems to protect the pool’s integrity from the unpredictable behaviour of the soil.
How clay movement impacts pool structure over time
Reactive clay doesn’t just shift once—it moves continuously over the years. As moisture content changes with rainfall, drought, or poor drainage, clay-rich soil expands and contracts, applying uneven pressure to any structure built above or within it.
For fibreglass pools, which are pre-moulded shells with limited flexibility beyond their engineered design, this movement can cause gradual deformation. Over time, owners may notice bulging walls, cracks in the shell, or even pool lifting, especially if the base slab or backfill was poorly designed or not suited to local soil conditions.
Melbourne’s seasonal climate makes this even more critical. A year of high rainfall followed by a dry summer can trigger noticeable ground shifts—making soil reactivity a long-term risk factor, not just a construction-phase concern.
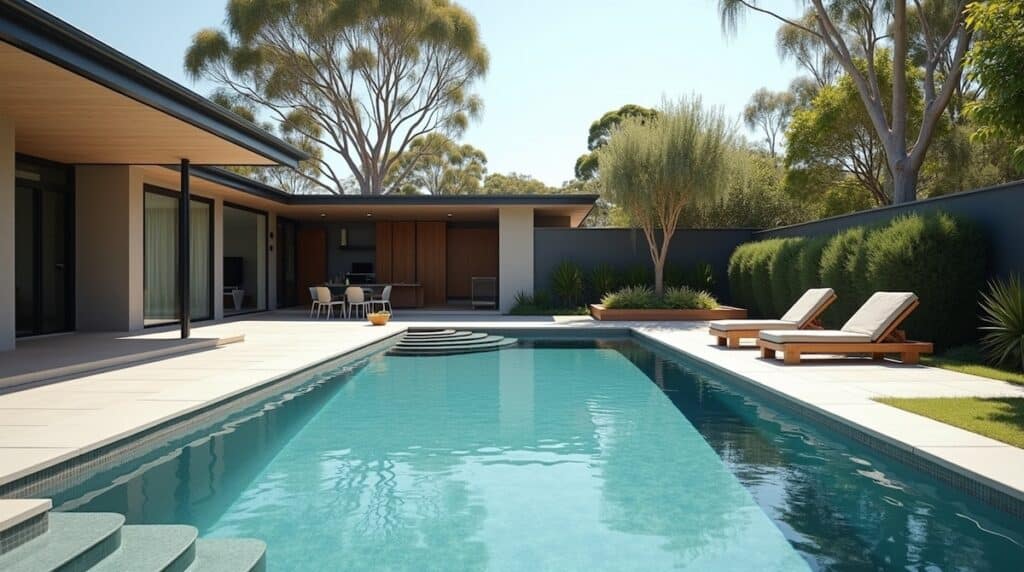
How Fibreglass Pools Respond to Reactive Soils
Structural flexibility: strength or weakness in Melbourne context?
One of the main selling points of fibreglass pools is their structural flexibility. Unlike rigid concrete, fibreglass can absorb minor ground shifts without cracking immediately. In theory, this makes them better suited to moderately reactive soils.
However, in Melbourne’s context—especially in high-reactivity zones—this flexibility can become a double-edged sword. When subjected to repeated or uneven ground movement, the pool shell may adapt too much, resulting in visible deformation like wall distortion or surface ripples.
So while fibreglass offers some buffer against movement, it’s not a substitute for solid preparation and soil-specific engineering.
Common issues reported: bulging, lifting, cracking
In Melbourne’s clay-dominant areas, fibreglass pools can experience a variety of structural problems when not installed with proper soil adaptation. The most frequently reported issues include bulging walls, especially along the sides where lateral soil pressure increases after rainfall. Lifting or “floating” can occur due to hydrostatic pressure building up beneath the pool in areas with poor drainage or high water tables. Hairline cracking is also common, often appearing near stress points like skimmer boxes or entry steps.
These symptoms often develop months or even years after installation, making them hard to predict without a thorough geotechnical analysis beforehand. While not always catastrophic, such damage can lead to expensive repairs—or even full shell replacement if left unchecked. These risks highlight the importance of site-specific construction strategies, not just shell quality.
Role of the slab and backfill in maintaining stability
In reactive clay zones like much of Melbourne, the quality of the slab and backfill is just as important as the pool shell itself. These two components form the foundation and support system that buffer the fibreglass structure against ground movement.
A reinforced concrete slab, designed specifically for the local soil class, distributes the load more evenly and reduces the risk of isolated pressure points that lead to bulging or lifting. Additionally, a high-quality backfill material, such as stabilised sand or crushed rock, ensures proper compaction and drainage—both critical in preventing hydrostatic pressure build-up.
Improper or rushed backfilling is a frequent cause of long-term instability. Without enough compaction, voids may form under or around the shell, inviting shifts, sags, or floating. For this reason, experienced Melbourne installers often schedule backfill in stages, with inspection checkpoints to confirm settlement.
How Melbourne-based installers adapt their methods
Local pool builders in Melbourne have developed specific techniques to counteract the challenges posed by reactive clay soils. Unlike generic installation methods, their approach begins with a comprehensive soil analysis, often involving engineers who classify the soil and recommend appropriate slab and drainage designs.
Once the soil is assessed, experienced installers may adjust the pool’s orientation to avoid tree roots, install subsurface drainage systems, or even reinforce the slab with pier supports in particularly unstable areas.
Moreover, some Melbourne specialists opt for staged backfilling with pressure-compacted layers, allowing for soil settlement monitoring before finalising installation. Others rely on hydrostatic valves to reduce upward pressure in flood-prone or poorly drained sites.
Ultimately, the success of a fibreglass pool in Melbourne’s clay-heavy environment hinges not just on materials, but on adaptability and local construction experience.
Can You Reinforce a Fibreglass Pool to Suit Melbourne’s Conditions?
Yes—but it requires thoughtful planning and engineering from the start. Reinforcing a fibreglass pool for Melbourne’s reactive clay conditions typically begins with the foundation. Rather than installing the shell directly into an excavated hole, most professionals recommend a structurally engineered concrete slab, often with steel reinforcement tailored to the local soil classification.
In areas with Class H or E soils, some builders go further by incorporating piling or pier supports, which anchor the slab deeper into more stable subsoil layers. This prevents uneven shifting due to seasonal ground movement.
Beyond the base, drainage design is critical. Installing subsoil drainage pipes and hydrostatic relief valves ensures that water does not accumulate beneath the pool—a common cause of lifting in clay-dominant suburbs.
Finally, experienced contractors will select the right backfill strategy, ensuring full compaction and moisture control. When these elements work together, fibreglass pools can perform reliably—even on Melbourne’s most challenging sites.
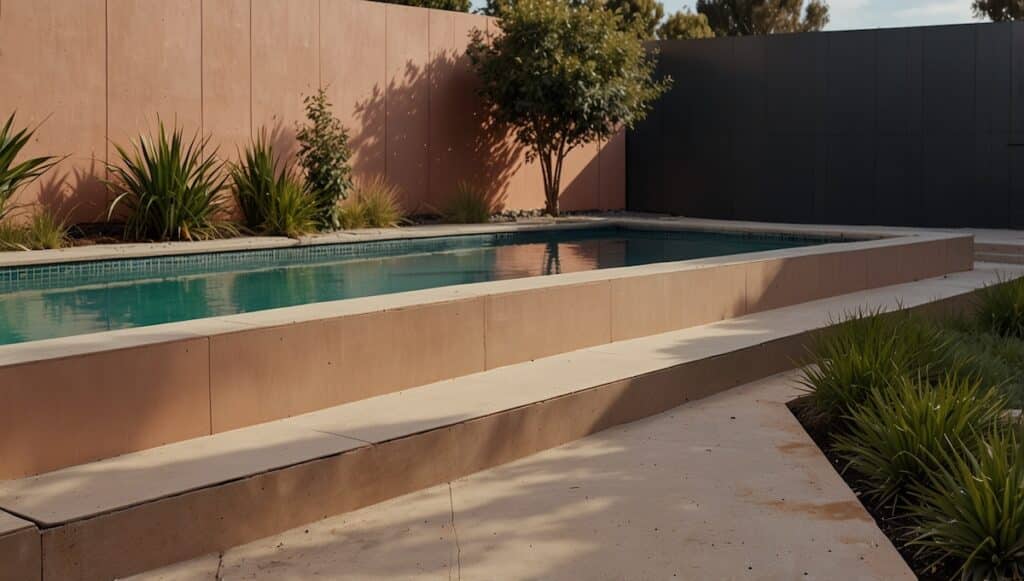
What Do Experienced Builders in Melbourne Recommend?
Installer insights: when to choose fibreglass over concrete
Seasoned builders in Melbourne often weigh several factors before recommending fibreglass over concrete. Site accessibility, budget constraints, and installation speed are common reasons to choose fibreglass—especially in suburban areas with limited space or difficult access where crane delivery is easier than setting up complex formwork.
Fibreglass also suits clients who prioritise a smooth, low-maintenance surface and quick installation timelines, as the shells are prefabricated and typically installed within a week.
However, these advantages only apply when the soil reactivity is moderate, and when the builder has the experience to implement reinforcements, such as slab engineering and drainage systems. Without these precautions, the risk of deformation increases over time.
Conditions where fibre is not advised
Experienced Melbourne builders are generally cautious when recommending fibreglass pools in extremely reactive soil zones, particularly where Class E soils or unstable slopes are involved. In these environments, the ground is highly prone to heave, shrinkage, and lateral movement—factors that can quickly exceed the flexibility limits of a fibreglass shell.
Other red flags include poor drainage or high water tables, which increase the risk of hydrostatic lift. Tight spaces with tree roots or unpredictable fill soils can also pose serious challenges. Sites where no proper slab or piling solution can be implemented due to cost or access constraints are another major concern.
In such cases, builders often suggest switching to concrete pools, which offer more design flexibility and are easier to reinforce structurally on unstable terrain. While fibreglass can perform well in many Melbourne locations, skipping a soil report or trying to cut corners on foundations can lead to costly consequences.
Examples of successful installs on difficult terrain
Despite the challenges of reactive clay, many successful fibreglass pool installations have been completed across Melbourne—even in high-risk suburbs like Bentleigh or Glen Iris. The key to success lies in site-specific adaptation and experienced execution.
In one case, a property in Malvern East with Class H soil saw a fibreglass pool installed atop a fully reinforced raft slab, paired with subsurface drainage and controlled backfill layering. After five years, the structure remains stable with no visible signs of distortion or movement.
Another example from Glen Iris involved a sloping block with clay over fill. The builder designed a piered foundation system to anchor the pool deeper into stable subsoil, allowing the fibreglass shell to remain unaffected by the reactive upper layers.
These cases show that with the right geotechnical input, engineering, and execution, fibreglass pools can be a viable solution—even on complex ground.
Choosing a fibreglass pool in Melbourne’s clay-rich environment isn’t just about selecting a shell—it’s about preparing the ground beneath it. While fibreglass offers flexibility, speed, and cost-efficiency, these advantages can quickly disappear without a proper understanding of the soil’s behaviour.
With a detailed soil assessment, engineered slab design, effective drainage, and an experienced local installer, fibreglass pools can indeed perform well—even in suburbs with Class H or E soil types.
Ultimately, material alone doesn’t guarantee success. It’s the combination of preparation, planning, and local adaptation that determines whether your pool will stand the test of time.
FAQ – What Melbourne Homeowners Ask About Clay Soil and Fibreglass Pools
Can a fibreglass pool crack because of Melbourne’s reactive soil?
Yes—but it’s rarely an instant failure. In Melbourne’s reactive clay zones, soil expansion and contraction can create long-term pressure on the pool shell. If not properly installed with a reinforced slab and well-compacted backfill, this can result in hairline cracks, especially around fittings or step areas.
However, with the right engineering and drainage solutions, these risks can be significantly reduced.
Is it better to install a concrete pool if my property is on clay?
It depends on the type and class of clay present on your property. In highly reactive zones (Class H or E), concrete pools are often recommended because they can be custom-reinforced on site to match soil conditions. This makes them structurally more adaptable than prefabricated fibreglass shells.
However, concrete pools come with higher costs, longer installation times, and more maintenance needs. If your site has moderately reactive soil and proper engineering is applied, fibreglass can still be a safe and durable choice.
Can I build a fibreglass pool in Glen Iris or Bentleigh?
Yes, but it requires strict adherence to engineering best practices. Both Glen Iris and Bentleigh are known for highly reactive clay soils, which can expand and contract significantly with seasonal changes.
To safely install a fibreglass pool in these suburbs, you’ll need a reinforced concrete slab, designed based on a geotechnical soil report. Effective site drainage is also essential to reduce hydrostatic pressure. Choosing a trusted builder with local experience in clay-heavy zones is equally important.
With these safeguards in place, many homeowners in these areas have successfully installed fibreglass pools that remain stable and fully functional over time.
Who is responsible if the pool lifts after installation?
Responsibility depends on the cause of the lifting and the contractual terms with your pool builder. In most cases, if the lift is due to poor installation, such as inadequate drainage or improper slab design, the installer or contractor may be liable under construction warranties.
However, if the homeowner neglects maintenance—like allowing stormwater to pool around the shell—or if unforeseen soil conditions were not disclosed or tested, responsibility can shift.
That’s why it’s essential to choose a builder who provides a comprehensive soil assessment and outlines structural protections in their warranty.