For Melbourne homeowners considering a new pool, one material keeps coming up: fibreglass. Whether you’re renovating a family backyard in Bentleigh or planning a first build in Preston, fibreglass pools are increasingly positioned as the smart, low-fuss solution—especially when timelines, cost, and soil conditions come into play.
Unlike concrete pools, which require months of staged construction and can be complex on sloped or reactive sites, fibreglass shells are pre-moulded off-site and craned in within days. This makes them highly appealing in Melbourne’s dense suburban blocks, where access is tight and neighbours are close.
Melbourne’s clay-heavy soils, strict council rules, and four-season climate all require a pool that’s both resilient and quickly installable. Fibreglass offers just that—plus lower maintenance needs and a smooth interior surface that’s ideal for busy family life.
If you’re weighing up your options, don’t miss our full guide on Concrete Pools in Melbourne (internal link)—a useful comparison if you’re still deciding between materials.
Why More Homeowners in Melbourne Are Choosing Fibreglass Pools
Across Melbourne’s expanding suburbs, fibreglass pools are becoming a go-to choice for families wanting a beautiful, functional pool—without the stress of a complex build. In areas like Bentleigh East, Werribee, or Rowville, where backyards are getting smaller and project timelines tighter, fibreglass offers fast, reliable installation with minimal disruption.
These prefabricated pools appeal especially to households that can’t afford to have builders on-site for months. The entire process—from permit to swim-ready—can take just weeks, compared to three to five months for custom concrete. For many time-poor families, that speed is decisive.
There’s also a growing desire to avoid heavy earthworks, particularly in clay-rich suburbs like Camberwell or Doncaster. Fibreglass pools require less intensive excavation and can often be installed with smaller crews and lighter equipment, reducing both noise and costs.
For a real-world look at why this trend is growing, see Why Bentleigh Families Are Choosing Fibreglass Pools in 2025 (internal link)—a local perspective grounded in practical experience.
Cost of a Fibreglass Pool in Melbourne: What You Need to Know
What influences the price: access, shape, landscaping
While fibreglass pools are known for their affordability compared to concrete, costs in Melbourne can vary widely depending on site-specific challenges. One of the biggest factors is access: in inner suburbs like Fitzroy North or Elsternwick, narrow laneways and tight blocks may require crane lifts, which can add thousands to your total cost.
Next is shape and size. Although fibreglass shells are prefabricated, choosing a longer or deeper model, or one with integrated spa zones, increases base price and installation logistics. Compact rectangular shells are the most economical; custom shapes or high-end finishes (like ceramic-coated interiors) add cost.
Finally, landscaping and integration affect the final bill. Installing decking, fencing, heating systems or water features can double or triple the project budget. In leafy suburbs such as Camberwell, blending the pool into a landscaped setting is often a priority—but it comes at a premium.
To go deeper into pricing breakdowns, visit our Fibreglass Pool Cost Melbourne guide.
Average installation costs in inner vs outer Melbourne suburbs
The cost of installing a fibreglass pool in Melbourne varies not just by size or style, but by postcode. In inner suburbs like Hawthorn, Clifton Hill, or South Melbourne, average installation costs typically range between $45,000 and $65,000. That’s due to limited access, higher labour costs, stricter council regulations, and the need for crane delivery in many terrace-style lots.
In contrast, outer suburbs like Craigieburn, Officer, or Werribee offer easier access and more open space, reducing logistical complexity. There, full installs often fall between $35,000 and $50,000, depending on landscaping and add-ons like heating or decking.
It’s also worth noting that soil type can shift pricing. Reactive clay zones in Glen Iris or Bentleigh may require additional slab stabilisation or drainage works, nudging prices upward even in suburban blocks.
While the shell cost may be fixed, local context—block layout, soil, suburb regulations—can significantly alter the final figure.
Fibreglass vs concrete: which is cheaper to build and maintain in 2025?
When comparing fibreglass and concrete pools in 2025, the cost difference is still significant—especially in Melbourne’s high-density suburbs where construction logistics are complex.
Fibreglass remains the more budget-friendly option. The prefabricated shell and faster installation timeline reduce labour hours, permit delays, and site preparation costs. A typical fibreglass pool may cost 25–35% less to install than its concrete counterpart, depending on location and design complexity.
Maintenance costs are also lower. Fibreglass surfaces are non-porous, which means fewer chemical treatments and less frequent cleaning. Concrete, by contrast, may require resurfacing every 10–15 years, along with more aggressive water balancing to prevent staining or algae buildup. To understand all the pros and cons, see our detailed comparison on the benefits of fibreglass pools vs concrete.
That said, concrete pools offer full design freedom—which can be worth the price for clients with complex sites or specific aesthetics.
For a detailed comparison beyond budget, see our Concrete Pools Melbourne guide (internal link) and weigh the trade-offs based on your property’s needs.
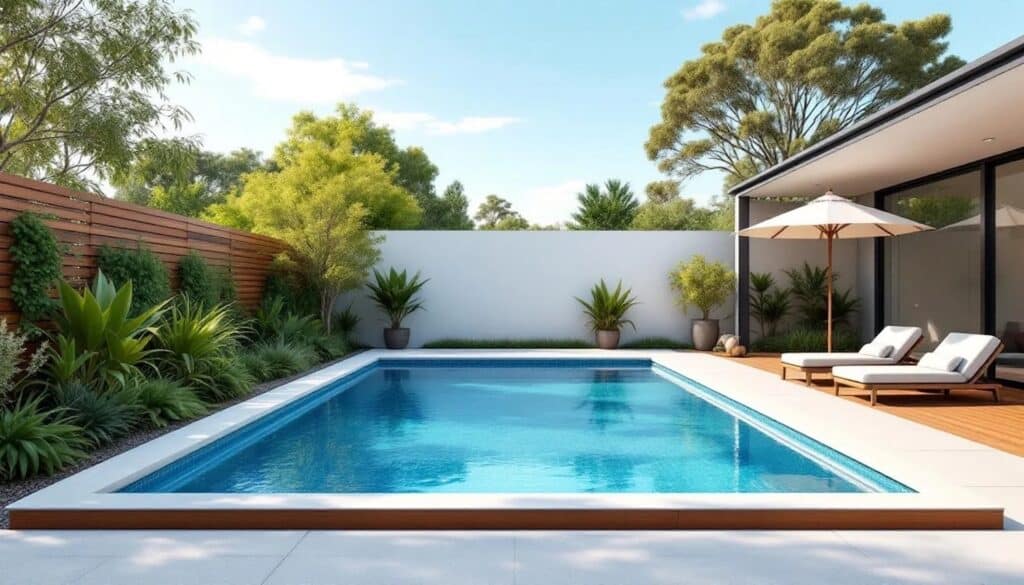
Is a Fibreglass Pool a Good Fit for Melbourne’s Clay Soil?
Understanding soil reactivity in Glen Iris, Camberwell and Bentleigh
Melbourne’s eastern suburbs—including Glen Iris, Camberwell, and Bentleigh—sit on highly reactive clay soils, which expand and contract with seasonal moisture. This movement creates structural challenges for any in-ground pool, especially when the soil shifts unevenly.
Before installation, a geotechnical assessment is typically required to measure soil reactivity and determine the risk level. Class M or H soils, common in these areas, demand a flexible yet stable solution—and fibreglass fits the bill. Its one-piece structure can flex slightly with ground movement, reducing the risk of cracking compared to rigid concrete shells.
In Glen Iris, for example, many homes are built on elevated clay-rich blocks, where traditional pools have required constant levelling or resurfacing. Fibreglass pools, paired with a reinforced base slab and proper drainage, offer a safer long-term investment in these reactive zones.
How fibreglass shells behave in reactive clay zones
Fibreglass pools are particularly well-suited to Melbourne’s reactive clay soils because of their monobloc structure and slight flexibility. Unlike concrete, which can crack under lateral pressure or soil movement, fibreglass shells are designed to move subtly with the ground—absorbing minor shifts without structural failure.
In reactive zones like Camberwell or Ashburton, the soil’s expansion during wet months and contraction during dry spells places strain on any in-ground structure. A fibreglass pool, when installed on a correctly engineered slab and supported by proper backfilling and drainage, is less likely to suffer from cracking, warping, or misalignment over time.
However, not all fibreglass pools are created equal. Thicker shells, reinforced ribs, and high-resin finishes perform better under duress than lower-end models. That’s why choosing a reputable local supplier—familiar with Melbourne’s soil conditions—is critical for long-term durability.
When designed and installed with local soil reactivity in mind, fibreglass pools offer an efficient, low-risk solution for challenging ground types.
Tips from Melbourne-based builders for soil prep and slab stabilisation
Melbourne-based pool builders with experience in reactive clay zones recommend a set of non-negotiable practices when preparing for a fibreglass installation. The key is preventing movement—not just reacting to it after the fact.
First, a reinforced concrete base slab is often preferred over gravel or sand beds. This creates a stable, level platform that distributes soil pressure evenly beneath the shell. In high-risk areas like Bentleigh East or Bulleen, builders may also include pier supports or screw piles at strategic points to further reduce shifting.
Next is drainage control. Reactive soil swells when wet, so directing water away from the pool shell is critical. This often involves subsoil drains, backfill with stabilised sand or flowable fill, and careful grading around the site to avoid pooling.
Finally, Melbourne experts advise against rushing backfilling. Letting the pool fill with water before compacting the backfill helps equalise pressure—protecting the shell from stress and bulging.
These strategies, when executed correctly, ensure a longer-lasting and trouble-free fibreglass pool install.
Local case studies: success stories and cautionary tales
Real-world examples from Melbourne suburbs illustrate both the benefits—and the risks—of installing fibreglass pools in reactive clay zones. When done right, the results are impressive. In Glen Iris, a family installed a 7m fibreglass pool on a sloped, clay-heavy block. Thanks to proper drainage, a reinforced slab, and patient backfilling, their pool has remained level and crack-free five years on.
In Camberwell, a similar project skipped soil testing and used basic bedding. After a season of heavy rain followed by drought, the pool shifted slightly, causing uneven tiling and fence misalignment. The repair costs exceeded $10,000—highlighting the importance of getting groundwork right from the start.
Another success in Bentleigh involved a narrow block installation where builders used pier footings and engineered backfill. The result: a low-maintenance pool that has handled seasonal soil movement with no visible damage.
These stories show that while fibreglass works well in clay conditions, it depends entirely on proper local preparation and experienced installers.
Comparing Fibreglass and Concrete Pools for Melbourne Homes
Installation timeframes in suburban blocks
When time is a major factor, fibreglass clearly outpaces concrete in Melbourne’s suburban settings. While both materials offer strong long-term value, the difference in installation speed can significantly impact homeowners working with tight schedules or seasonal deadlines.
A fibreglass pool—once the permit is approved—can be fully installed and swim-ready in as little as 2 to 4 weeks. This includes excavation, delivery, placement of the shell, connection of services, and backfill. In suburbs like Bentleigh East, Doncaster, or Altona, where backyard access allows crane delivery, projects move even faster.
In contrast, concrete pools follow a much longer process: excavation, steel reinforcement, plumbing, spraying, curing, tiling, and landscaping. In Melbourne’s climate, where weather delays are common, this process can stretch to 3–5 months or more.
For homeowners in fast-growing areas with young families or new builds, the rapid turnaround of fibreglass pools makes them a practical choice that aligns with modern project timelines.
Maintenance and lifespan under Melbourne’s climate
In Melbourne’s climate—marked by seasonal extremes, tree-heavy suburbs, and frequent rain—fibreglass pools have a clear advantage in maintenance and long-term performance. The smooth, non-porous gelcoat surface resists algae, staining, and chemical absorption far better than concrete, which is inherently porous and more reactive to pH swings.
Because fibreglass surfaces are slick and sealed, they’re easier to clean, require fewer chemicals, and don’t need interior resurfacing for at least 20–25 years. In contrast, concrete pools often require acid-washing every few years and resurfacing within 10–15 years, particularly in leafy areas like Kew or Ivanhoe where organic debris is common.
Maintenance systems also differ: fibreglass pools tend to support better circulation flow, with fewer internal ledges or steps that trap dirt. Combined with solar covers and automatic chlorinators, they’re ideal for low-touch upkeep.
While both pool types can last decades, fibreglass pools often deliver a lower total cost of ownership and fewer surprises—especially when matched to Melbourne’s unique environmental demands.
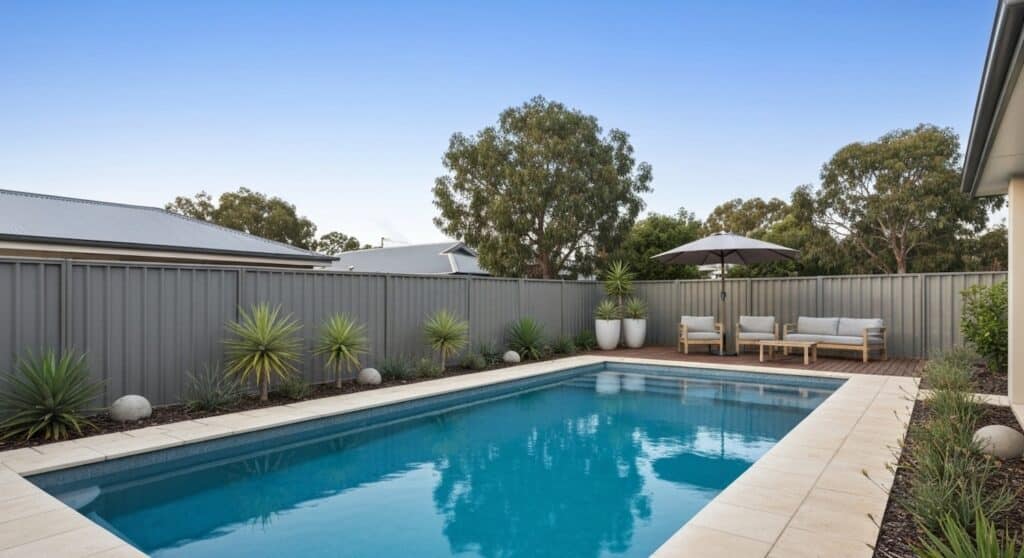
Installation Process for Fibreglass Pools in Greater Melbourne
Typical site access issues: terraces, shared driveways, narrow lanes
In many of Melbourne’s inner and middle-ring suburbs, tight site access is one of the biggest challenges when installing a fibreglass pool. Areas like Carlton, North Fitzroy, and Brunswick are known for their narrow laneways, compact blocks, and shared boundaries—factors that demand precise planning and experienced crews.
Because fibreglass pools arrive as one-piece shells, they must be craned or carefully manoeuvred into place. That means builders must assess overhead powerlines, tree clearance, street parking, and whether a mobile or tower crane will be required. In some cases, temporary removal of fencing or partial roof deconstruction is necessary to achieve a safe drop-in zone.
Shared driveways and terrace homes also complicate logistics. Homeowners may need to negotiate with neighbours or council for temporary easements or traffic control permits—especially in denser areas.
To better understand the solutions for tight sites, see Pool Access Strategies for Carlton and North Fitzroy Homes (internal link)—a guide built around real access scenarios in heritage suburbs.
Delivery and handling of the fibreglass shell
The delivery of a fibreglass shell is a critical stage in the installation process—one that requires coordination, preparation, and on-site precision. In Melbourne, the process usually begins with transport from regional manufacturing centres in Victoria, followed by scheduled drop-off directly onto the prepared site or staging area.
Shells are typically delivered via flatbed trucks and require a crane or telehandler to lift them safely into the excavation. Builders in suburbs like Glen Waverley or Essendon must anticipate nearby trees, slopes, or property boundaries that could complicate access. The lifting process is highly choreographed to avoid damage to the shell or surrounding structures.
Handling is also about protection. Fibreglass shells must be kept dry and level, and movement should be minimised to avoid stress on structural ribs. Most reputable Melbourne installers will use slings, spreader bars, and experienced riggers during the lift phase.
With proper delivery and careful placement, this stage can be completed in under an hour—bringing your pool project visibly to life in a single day.
Installation timelines: what to expect week by week
A key advantage of fibreglass pools in Melbourne is the predictability of the installation timeline. While weather or access can introduce slight delays, most projects follow a well-defined weekly rhythm.
Week 1 – Site preparation and excavation
Once permits are approved, excavation begins. In suburbs like Donvale or Glen Huntly, where soil conditions can vary, this phase includes setting base levels and managing spoil removal.
Week 2 – Shell delivery and placement
The fibreglass shell arrives and is lowered into place. Builders check for level alignment, install plumbing, and begin backfilling to stabilise the structure. With ideal access, this can happen in a single day.
Week 3 – Coping, fencing, and electricals
This week focuses on edge finishes, temporary or permanent fencing (to meet safety regulations), and setting up lighting or filtration systems.
Week 4 – Handover and water balancing
Final inspections take place. Once filled, the water is balanced, and the system is tested before handover. Many homeowners in Melbourne are swimming within 30 days of excavation start.
How Durable Are Fibreglass Pools in Melbourne Conditions?
If you’re looking for a pool that balances cost, speed, and adaptability, fibreglass is a strong contender—especially in a city like Melbourne where soil reactivity, climate variation, and block access often complicate traditional builds.
Fibreglass pools deliver fast results with minimal site disruption, making them ideal for busy families or tight suburban lots. They perform well in clay-heavy soils (when properly installed), require less maintenance than concrete, and offer a sleek, durable surface that lasts for decades.
That said, they’re not a one-size-fits-all solution. If your project calls for fully customised shapes, complex water features, or extensive landscaping integration, concrete may be a better fit.
Not sure which path is right for you? Explore these related pages to inform your decision:
– Pool Builders in Melbourne
– Concrete Pools Melbourne
– Fibreglass Pool Cost Melbourne
A tailored pool starts with a local strategy. Work with professionals who understand Melbourne’s terrain, councils, and climate—and your pool will reflect that smart foundation.
Fibreglass pools are built to last—and in Melbourne’s climate, their durability is one of their strongest selling points. With high UV exposure in summer, cold winters, and seasonal storms, pools in this region must resist expansion, fading, and structural stress.
A well-manufactured fibreglass pool can last 25–30 years or more, especially when paired with quality filtration and chemical care. The gelcoat finish resists algae growth, staining, and abrasion—unlike porous concrete, which is more susceptible to water penetration and surface degradation.
Rain and wind exposure don’t typically affect the shell itself, but poorly drained soil or movement under the slab can shorten lifespan. That’s why local installers in suburbs like Wheelers Hill or Montmorency stress drainage and base stability as key to longevity.
Most reputable fibreglass pool brands offer structural warranties of 25 years, backed by performance in real-world Melbourne conditions.
For a deeper dive into warranties and expected lifespan, explore our guide: Lifespan and Warranty of Fibreglass Pools.