Building a concrete pool in Melbourne isn’t just about pouring concrete and filling a hole—it’s a structured, multi-phase process that must take local climate, soil types, and council regulations into account from day one. Unlike fibreglass installations, which follow a more templated path, concrete pool construction demands technical precision tailored to each unique site.
Melbourne presents specific construction challenges: reactive clay in areas like Coburg, steep gradients in Eltham, or sandy soil near Brighton can all affect timelines and techniques. Add to this the city’s unpredictable weather and council permit requirements, and it becomes clear why working with a local expert is essential.
This step-by-step guide walks you through each phase of the construction process—from initial planning to the final fill—so you can anticipate what’s involved and make informed decisions at every stage.
Before the first shovel: Technical and local planning
Site analysis in Melbourne: access, slope, soil quality
Before any concrete is poured, a detailed site analysis is essential to ensure the project is both structurally feasible and logistically efficient. In Melbourne, local conditions can vary dramatically—even within the same council zone—so evaluating the terrain early helps avoid costly delays later.
Suburbs like Eltham, with their steep, bush-covered blocks, or Glen Iris, where rear access can be limited by narrow laneways, require customised excavation and delivery plans. Soil composition is another critical factor: reactive clay, common in northern suburbs, can shift with moisture and may demand deeper excavation or additional reinforcement. Conversely, sandy soils closer to the bay, like in Brighton, might need stabilisation to prevent wall collapse during digging.
Access points, tree coverage, proximity to neighbouring structures, and water tables all come into play when planning the build. A thorough site study ensures your concrete pool design aligns with Melbourne’s real-world building constraints—saving both time and money before construction begins.
Permits, regulations, and lead times specific to Melbourne
Securing the right permits is a critical early step in any concrete pool project—and in Melbourne, the requirements can vary significantly between councils. From Glen Eira to Manningham, local authorities each have their own processes, documentation standards, and approval timelines.
In most cases, you’ll need both a planning permit and a building permit before excavation can begin. Factors like property setbacks, existing structures, heritage overlays, and tree protection zones all influence whether additional documentation or assessments are required. It’s not uncommon for this stage to take 4–8 weeks, depending on the suburb and time of year.
Melbourne homeowners are encouraged to start this process early and consult with local professionals familiar with council expectations. For a detailed breakdown of what your specific council may require, see Which Council Permits Do You Need for a Pool in Melbourne? (internal link).
Taking this step seriously avoids costly delays—and ensures your project stays compliant with Victoria’s building regulations from the outset.
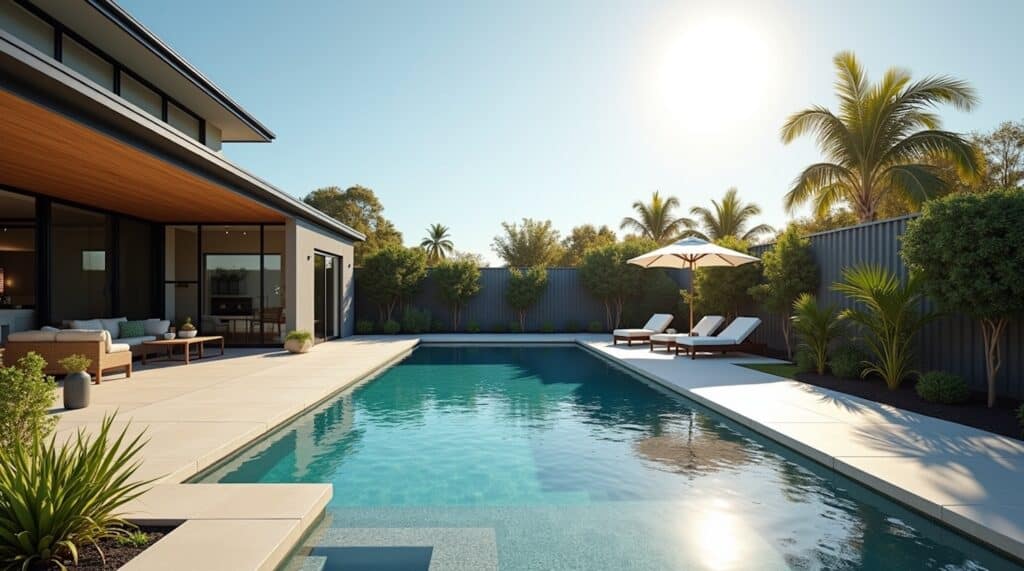
Excavation: Adapting the dig to Melbourne’s terrain constraints
Excavation might seem straightforward, but in Melbourne, the digging phase must be tailored to the specific conditions of the site. Soil composition, slope, and even neighbourhood access rules all influence how the earthworks are carried out—and how long they’ll take.
In areas like Coburg, reactive clay can complicate excavation, requiring deeper digs and engineered footings to stabilise the structure. In contrast, Brighton’s sandy soils pose a risk of sidewall collapse, demanding careful shoring or temporary supports during the process.
Excavation depth also depends on whether the design includes features like deep-end zones, integrated spas, or stepped entries—all of which must be carved precisely. Limited access via narrow driveways or laneways may require small-scale equipment or hand excavation in dense urban blocks.
While this phase typically lasts just a few days, it’s one of the most crucial steps in the concrete pool construction process. Getting it right sets the foundation—literally—for everything that follows.
Formwork and steelwork: Building the base for Melbourne’s changing climate
Weather management: rain, wind, curing windows
Once excavation is complete, the formwork and steel reinforcement define the pool’s shape and strength—but this phase is heavily influenced by Melbourne’s unpredictable weather. Sudden rain, high winds, or even extended heatwaves can all disrupt the timeline and compromise structural quality if not carefully managed.
Melbourne’s rainy months—typically late autumn and early winter—can flood excavation pits or wash away freshly placed formwork. Delays aren’t just inconvenient; they may require re-setting steel or replacing timber forms altogether. Wind is another hidden risk, as exposed rebar and mesh can be hazardous to workers and difficult to stabilise on sloped or elevated sites.
Temperature fluctuations also affect the curing process. Cold days slow down setting times, while hot, dry winds can cause surface cracking if moisture evaporates too quickly. Local builders usually plan this phase during milder weather windows and may use curing blankets or wind breaks to control conditions.
Mastering these variables is key to creating a structurally sound base that holds up over decades—especially in Melbourne’s climate-diverse suburbs.
Concrete pour: Timing, quality, and local expertise
Why daily temperature affects concrete curing
Concrete may seem like a strong, no-fail material—but the day you pour it matters more than many realise. In Melbourne, where temperatures can swing quickly even within a single day, the weather during the pour directly influences how well the concrete sets, bonds, and ultimately performs.
If poured during high heat, concrete may dry too fast, leading to surface cracking or internal weaknesses. On the other hand, cold or damp days can slow the curing process, preventing the concrete from reaching optimal strength in time. This is especially important in suburbs like Doncaster or Ringwood, where sudden weather shifts are common.
Local builders mitigate these risks by monitoring both ambient temperature and surface temps. Additives may be used to speed or slow the set time, and in some cases, early morning or late afternoon pours are scheduled to avoid extreme midday heat.
Understanding this timing is part of what separates general builders from concrete pool specialists in Melbourne’s climate-sensitive construction scene.
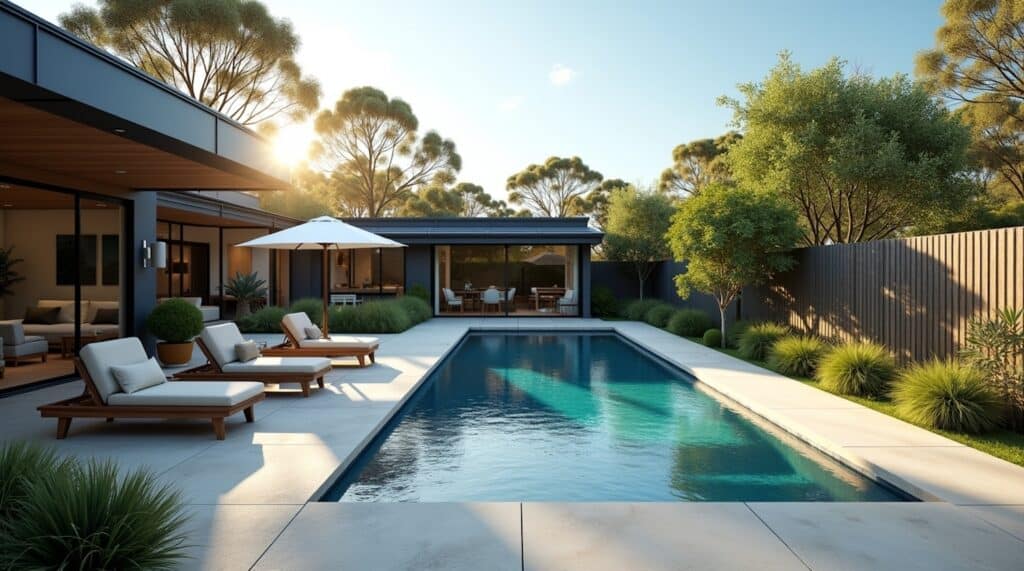
Waterproofing, interior finish, and coping: Local usage-driven choices
Popular finishes in Melbourne: quartz, tile, render
Once the concrete shell is cured, choosing the right interior finish becomes a key decision—not just for looks, but for performance and long-term maintenance. In Melbourne, where pool use spans all four seasons and environmental conditions vary by suburb, certain finishes have emerged as favourites.
Quartz aggregates are widely used for their balance of durability and texture. They’re especially popular in eastern suburbs like Balwyn and Camberwell, where homeowners prefer a refined but natural look.
Glass or ceramic tiles are chosen for high-end projects, particularly in minimalist designs across suburbs like Toorak or South Yarra. They’re easy to clean and create a striking visual effect, though they often come with higher installation costs.
Rough or coloured renders remain a cost-effective and versatile option, especially for larger pools. These finishes offer broad colour choice and a softer underfoot feel—ideal for family-oriented areas like Glen Iris or Surrey Hills.
The finish you choose not only defines the pool’s aesthetic—it also affects how it weathers, resists staining, and responds to cleaning over time.
Adapting for four-season use: heating, covers
In Melbourne, a well-designed concrete pool isn’t just for summer—it’s increasingly expected to function comfortably throughout the year. Adapting your pool for four-season use involves more than aesthetics; it requires smart decisions about heating systems, insulation, and protective coverings.
Integrated heating—whether via heat pumps, solar panels, or gas systems—is now a standard inclusion in many new builds across eastern suburbs like Donvale and Camberwell. The choice often depends on block orientation, access to sun exposure, and frequency of use.
Automatic pool covers or thermal blankets are also gaining popularity, not just for heat retention but to reduce debris and evaporation during Melbourne’s windy autumns and cool winters. Combined with proper insulation around the concrete shell, these features make it easier to maintain stable water temperatures and reduce operating costs year-round.
For more on system types and what works best in Melbourne’s cooler zones, see How to Heat a Pool for Year-Round Use in Melbourne’s Eastern Suburbs (internal link).
Site cleanup and fill-up: Final but often underestimated steps
With the structural work and finishes complete, many homeowners assume the job is done—but the final phase of construction is just as important. Site cleanup and initial pool filling mark the transition from build to operation, and when mishandled, they can delay usability or affect long-term water quality.
Cleanup involves removing excess materials, debris, concrete dust, and any formwork remnants left around the pool area. This not only improves safety but also prepares the space for landscaping or deck installation. In tight Melbourne suburbs like Fitzroy or Prahran, where backyard space is limited, a clean, clear site is essential for completing the project efficiently.
Filling the pool should be done carefully, with attention to flow rate and filtration. It’s also the first opportunity to balance water chemistry and test all equipment under real conditions. Skipping these steps or rushing through them can lead to surface stains, pump strain, or chemical imbalances from day one.
Treating this final stage with care ensures your concrete pool starts its life clean, safe, and ready for long-term use.
Average project timeline for concrete pools in Melbourne
Typical example from the Boroondara area
While every project is unique, understanding how long a concrete pool takes to build in practice helps set realistic expectations. In Melbourne’s Boroondara area—which includes suburbs like Kew, Camberwell, and Hawthorn—site access, permit processes, and soil types all influence the construction timeline.
A standard residential project here typically spans 10 to 14 weeks, broken down into key phases:
Planning and permits: 3–5 weeks, depending on council response times
Excavation and steelwork: 1–2 weeks
Concrete pour and curing: 1 week
Waterproofing, tiling, coping: 2–3 weeks
Cleanup, fill, and equipment commissioning: 1 week
Buffer time for weather delays or inspections: 1–2 weeks
Properties in Kew and Hawthorn often involve stricter overlays or access restrictions, adding time at the permitting stage. But with experienced local builders, most pools in this area are delivered within 3 months.
For a closer look at council expectations and timelines, see Understanding Pool Permits in Boroondara Council (Kew, Camberwell, Hawthorn) (internal link).
What happens after construction? Care and value retention
Completing the build is only the beginning. Once your concrete pool is operational, a consistent care routine is essential—not just for water quality, but to protect your long-term investment. This is especially true in Melbourne, where climate, tree coverage, and seasonal use patterns can vary dramatically from one suburb to another.
Routine maintenance tasks like chemical balancing, skimming, and filter cleaning should begin as soon as the pool is filled. Concrete surfaces, while durable, are porous and can stain or degrade if not treated properly from day one. Post-construction is also the perfect time to set up heating systems, automation tools, and maintenance schedules.
Many homeowners choose to work with professional services for the first few months to ensure proper setup and learn best practices. This proactive approach helps preserve the surface finish, minimise repairs, and boost the long-term property value of your outdoor space.
For a complete breakdown of maintenance recommendations, see Maintenance tips for concrete pools (internal link).
Building a concrete pool in Melbourne is a complex, multi-stage process that demands local expertise, strategic planning, and precise execution. From navigating council permits to adapting to climate-driven construction windows, every phase requires attention to detail—and a clear understanding of how Melbourne’s unique conditions shape the project.
By working with experienced professionals and understanding what happens at each step, homeowners can make informed decisions, avoid costly missteps, and ensure that their pool not only looks stunning but also performs reliably for years to come.
Whether you’re planning a build in Brighton, Boroondara, or beyond, the key to a successful project lies in preparation, local insight, and a commitment to long-term care.